A Rocket Press for Small Tubes
Introduction
Hand ramming small devices such as black-powder fountains and rocket motors is a great way to get started making fireworks. But as you advance you will find that consolidating pyrotechnic compositions by hand ramming will only get you so far.Some compositions--such as whistle and strobe rocket fuels--are impact sensitive, so hand ramming is out of the question due to safety considerations. Or perhaps you suffer from carpal-tunnel syndrome, and all that hand hammering is simply painful. Or perhaps you want to construct a fireworks device or use a type of tooling that requires consolidation of the pyrotechnic composition with greater force than is possible with hand ramming.
For these and other reasons, at some point in our pyro-hobby career a press becomes a necessity. With a press you will be able to:
- Safely consolidate impact sensitive compositions
- Safely consolidate compositions which contain rough, sparking, metal particles
- Quickly and completely consolidate fuel increments in one stroke
- Easily exert the force required by larger tooling, like comet pumps and star plates
- Rapidly produce a wide variety of devices such as spolette time fuses, rocket motors, fountains, stars, and comets

A Simple, Inexpensive, Modified Arbor Press, Pressing 1/2-Inch Tooling, on a Homemade Force Gauge
Among their other virtues, presses provide greatly improved mechanical advantage than is available when hand ramming.
If a 1/2-inch ID tube is hand rammed with composition, it is possible to develop the equivalent of approximately 1,000 pounds-per-square-inch (PSI) of pressure on the composition.
When the above press is used on that same device, it is easy to apply 1,750 pounds of force to the surface area of the composition, which equates to 9,000 psi (pressure) on the composition. Many rocket builders press the fuels in their higher-power motors at that 7,500-9,000 PSI pressure. So, the press allows us to very easily apply this much higher amount of pressure to our devices.
That tremendous difference in pressure on the composition results in much greater compaction of the composition and the creation of a much more solid fuel "grain." Some fuels only perform well when they are pressed at these high pressures, and greater compaction results in more fuel being consolidated in the tube.
Often, obtaining a press can be a financial challenge for a developing fireworker. Some more-advanced presses can cost between $500 and $1,000. But there are more economical options for beginners. The simple, easily adapted press shown in this project will cost less than $75 total--much more affordable.
This press will be well suited to pressing devices up through 5/8-inch ID, larger than any consumer fireworks available. This press is also portable and easily transported, making it perfect to take to local and national fireworks club events.
Starting with a One-Ton Arbor Press
An arbor press is a mechanical shop-tool designed to do jobs which require these kinds of forces and pressures, such as installing or removing bearings from machine parts. A hand-operated lever turns a shaft with gear teeth on it. That gear operates a vertically-moving ram which applies force to the machine part. Force applied to the lever is mechanically multiplied into a resulting higher force applied by the ram.A one-ton press is rated to apply up to 2,000 pounds of force on something such as rocket tooling. That would be the same as piling 2,000 pounds of bricks on top of the tooling.
That amount of force then becomes pressure, rated in PSI (pounds per square inch), when it is applied to a particular surface area. The end of a 1/2-inch diameter, flat-ended rocket rammer with no hole in its end has a surface area of about 0.2 square inches. If the press's rated force of 2,000 pounds is applied to that 0.2 square inches, we get a pressure of 2,000 / 0.2 = 10,000 pounds per square inch. That is more pressure than most rocketeers ever apply to the fuel in a motor.
As the size (diameter) of the rammer increases, the maximum force that can be applied to the rammer by the press remains the same--2,000 pounds. However, the pressure (PSI) goes down because of the larger surface area of the end of the rammer. For example, suppose the rammer is 5/8-inch in diameter (instead of 1/2-inch). Its surface area is 0.3 square inches (instead of 0.2 square inches) and we get a pressure of 2,000 / 0.3 = 6,667 PSI (instead of 10,000 PSI).
The basic one-ton arbor press we will be adapting for our project can be found for sale here.
Unpacking and Preparation
The press comes assembled except for the loose shaft and lever-arm assembly, and the collar which will hold the shaft in place eventually.
One-Ton Arbor Press, Packed and Unpacked

Additional Parts Removed From the Press
The ram will easily slide up and out of the press body. There is a small metal shim inside the hole that the ram was inserted into. This shim should be removed and set aside in a secure place. The base plate should also be removed at this time.
All of these parts will have a layer of grease on them, applied by the manufacturer to prevent rusting in shipment. Use paper towels to remove as much of the grease from them as possible. Do not remove the grease from inside the hole the ram slides through, though.

Four "Feet" on the Bottom of the Press
You'll notice that the bottom of the press is not solid and flat, but has four "feet" which must be supported for the press to rest solidly on its work surface.
You can also see where the two 5/8-inch mounting holes are drilled through the press's base. These holes are designed to have owner-provided bolts installed through them to solidly attach the press to a workbench.
The specifications list the maximum height of an item which can be worked on by this press, as it comes out of the box, as 5-1/2-inches. The focus of our efforts in modifying this press will be to increase that specification by raising the press on a hand-made base. When we are finished, we will have increased the maximum height of an item we can press to over 13-1/2 inches.
Modifying the Press to Meet Our Needs
The picture below illustrates how we will achieve this.
New Wood Base Installed on Arbor Press
All the lumber and hardware used in this project is readily available at local hardware and lumber stores.
You can see that the new wood base is constructed of six pieces of wood, and that the base is secured to the workbench by two 1/4-inch bolts, with nuts and washers under the workbench. The arbor press is attached to the wood base with four 1/2-inch x 12-inch threaded rods, with accompanying nuts, washers and lock-washers.
The threaded-rod bottom nuts and washers are recessed into the bottom piece of wood, so the base can sit flat on the workbench.
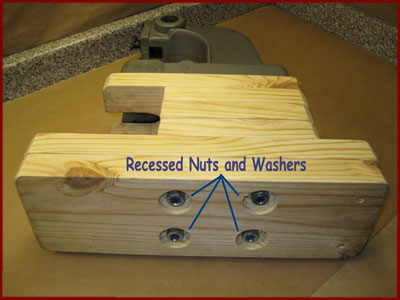
Bottom of New Wood Base
The first press modification that needs to be done is drilling the two additional holes in the base of the press to accommodate the front pair of 1/2-inch threaded rods. The two new holes should be as wide apart as the original two 5/8-inch holes in the press's base, and should be centered in the narrow, flat, machined area shown in the photos below.
Warning: Drilling metal is not as safe and easy as drilling wood. Drill bits can grab in metal, potentially twisting the drill and/or the piece being drilled. Be careful when doing this drilling. Wear leather gloves. Follow the instructions below. If you have never drilled metal before, consider getting some guidance from someone who has. Getting hurt would take all the fun out of a project like this.

Location of Two New ½-Inch Holes Drilled in Press Base

New Holes Laid-Out and Drilled from Bottom of Press
It is easiest to lay-out and drill the holes from the bottom of the press. When it is being drilled, the press should be securely anchored to prevent it from moving. The holes should be drilled slowly, with very sharp drill bits, starting with small bits, and gradually working upwards in bit size, drilling the holes gradually larger until 1/2-inch is reached.
Wobbling the 1/2-inch bit in the hole as the drill is running will slightly enlarge the holes and allow the threaded rod to slide through them easily. But be careful when doing this in case the drill bit grabs in the metal, as previously mentioned.
Making the New Wood Base
The wood base is going to be made out of 1-1/2-inch x 5-1/2-inch lumber. Six feet of this wood will be needed. Although these dimensions are standard for "2x6" construction lumber, typically 2x6's construction lumber comes in spruce or white pine wood. That wood is not strong enough for our purposes as we make this press base. It is soft wood and will bend and break relatively easily.The wood shown in the photos above is southern yellow pine, or SYP for short. In the USA Midwest and elsewhere, this wood is commonly available as 2x8's and larger construction lumber used for floor joists and roof rafters. This wood is strong and hard, and it will not flex or break easily. Other areas of the country use different wood species for such construction framing where strength is required. Just inquire at your lumber yard as to what lumber is used for floor joists in home construction, and use that lumber. Oak or other dense hardwoods would also be very acceptable lumber for this project.
Note: If you have a roof-truss manufacturing plant in your area, you might ask them if they have any 2x6 SYP scraps you can have. Many roof trusses do use 2x6 Southern Yellow Pine for some of their members.
Whatever 1-1/2-inch-thick lumber you end up using, rip 6-feet of it to the desired 5-1/2-inch width, if it is not already that width.
Note: I ripped SYP 2x8 lumber, which is 7-1/4" wide, down to the desired 5-1/2-inch width, for my base. Why not just use the full 7-1/4-inch width? In the photos of the finished press, you'll see a nice extension handle installed on the arbor press, instead of the handle it originally came with. This extended handle needs to be able to rotate past the side of the base, so the narrower 5-1/2-inch wide lumber is needed to allow that.

The Six Pieces of Wood that Make Up the New Base

Dimensions of Top Layer of Wood Base, #6
The top piece of wood is labeled #6, and is the piece the arbor press will sit directly on. Its dimensions are shown above. The 1-3/4-inch-wide slot is rounded to match the similar slot in the press.
The 5/8-inch drilled holes are located and spaced to match the holes in the arbor press. To ensure that they do (even if you got off of the specified dimensions a little when drilling the two new holes in the arbor press earlier), it is best to use the actual holes in your press as a guide for marking the spots to drill the holes in these pieces of wood.
5/8-inch holes will allow a little leeway when fitting all the boards together, under the press, and running the 1/2-inch threaded rods through all the holes.
The 1/2-inch rounded corners simply soften those edges. All corners and edges are smoothed with some sandpaper.
A circular saw, a saber-saw, and an electric drill are to be used to cut and drill the wood to these dimensions. A drill press is ideal for drilling the holes in the wood, since it can ensure that the holes are drilled perfectly straight through the lumber.
Wood pieces 3, 4 and 5 should have holes drilled in them which match the holes in #6. Their back ends will line up with the back end of piece #6. These three pieces are only 7-7/8-inch long, and they only have their back corners clipped (rounded), not the front ones.

Wood Base Pieces 3, 4 and 5
Pieces 1 and 2 are as shown below. The press hole pattern is the same as shown for the top piece, #6, except the back holes are centered 5-3/4 inches from the back, instead of 3-1/4 inches.
It is easiest to recess the holes in the bottom of piece #1 before drilling the 5/8-inch holes all the way through the board. Drilling the recesses, and then all the 5/8-inch holes, is easily done with "spade bits."

Wood Base Pieces 1 and 2

Spade Bits Used to Drill Holes and Recesses in Wood
Now that you have all the pieces of lumber cut, drilled, and sanded smooth, it's time for a trial-fit of the whole assembly to verify that everything is aligned properly and the pieces all fit together well.

New Base Pieces Ready to be Trial-Fit Together

Trial-Fit of All New Base Pieces
Once you have verified that all the pieces of the new base fit together as shown above, use 2-1/2-inch drywall screws, and good-quality construction adhesive, to join all the wood pieces together.
It can make that job easier, and will help prevent splitting the lumber, if the wood is pre-drilled for the screw-holes prior to applying the glue. Drilling and screwing the boards from their bottoms, starting with boards 6 and 5, and working through 4, 3, 2, and finally 1, will keep all the screw heads hidden once the base is turned right-side-up.

Drilling, Gluing, and Screwing the Boards Together, One at a Time

The Last Board, #1, Attached to the Base Assembly
Once the base is glued and screwed together, install the press on the base assembly using the 1/2-inch x 12-inch pieces of threaded-rod, with the washers, lock-washers, and nuts. Securely tighten the rod's nuts to compress the whole wood assembly together as the glue dries.

Glued and Screwed-Together Base, with Arbor Press Bolted Tightly On It
After the glue has dried completely, remove the arbor press and threaded rods, and give the base a good coat of black paint. The paint will seal moisture out of the wood base, and prevent swelling, shrinking, warping, or cracking. Also, black hides stains from pyrotechnic composition best.
Note: Of course, if you're only planning to press red-iron-oxide-catalyst whistle fuel, you may wish to paint your press base a matching shade of pink. Yeah, right.

New Wood Base Painted Black
Once the paint is dry, the press can be bolted back onto the base.

Press Bolted on Painted Wood Base
The metal cover over the shaft and ram recess has four attachment bolts, and two adjustment bolts with locknuts on them. Remove the attachment bolts and the cover.

Press Recess Cover and Bolts Removed
Use a small brush to spread a thin film of grease inside the areas where the shaft will turn, the area where the ram slides up and down, in the teeth of the shaft gear, and in the teeth of the ram. Also apply a thin film of grease on all three of the flat surfaces of the ram that will slide through the press.
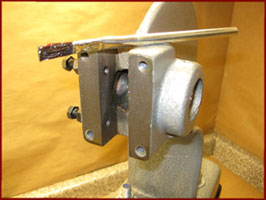
Grease Brushed onto Bearing Surfaces
Slide the shaft and lever arm assembly into position through the right-side hole first. Rotating the shaft as you do this will facilitate its positioning.

Shaft Installed in its Location
Put the bottom press-plate into a temporary position as shown below. Use it to support the ram in place as the ram is pushed into the recess. Mesh the ram's teeth with the teeth on the shaft gear.

Ram in Position and Supported by Press Plate
The two front adjustment bolts on the front cover and the two adjustment bolts on the side of the press should be backed out far enough that the ram can travel easily up and down.

Thin Metal Shim Held in Position with a Spot of Grease
A spot of grease will hold the thin metal shim in place in its position in the recess of the front cover. Install the front cover with its four bolts.

Front Cover and Shaft Locking-Collar Installed and Tightened
Now install the locking collar on the left side of the shaft as shown above to hold the shaft securely in position within the press. Securely tighten the set screw on the locking collar.
Note: If that collar is at all loose, and the press is picked up by the lever arm, the whole shaft and lever arm assembly can slide out of the press. The rest of the press (that would be the heavy part) can land on your foot. Ouch! Never lift the press by the lever arm.
The two side adjustment bolts are designed to just barely rub on the ram as it moves up and down, thereby limiting side-to-side movement as the ram travels. Similarly, the two front adjustment bolts press the shim against the ram--ever so slightly--to limit ram movement in the front-to-back direction.
These bolts should be tightened, one at a time, until the ram stops sliding easily up and down. Then the bolt should be backed off slightly until the ram just slides easily, and the locking nut tightened down to hold the bolt in place securely.
Once the bolts have been adjusted correctly, the ram will slide up and down easily, but will have very little side-to-side or front-to-back play.

Adjustment Bolts Correctly Tightened and Held in Place with Tight Lock-Nuts
Near the beginning of this project, the lever arm that comes with the press was shown. This arm is relatively short, and must be moved back-and-forth through the hole in the shaft as different height devices are pressed.
One really nice additional modification, which our new base makes possible, is the replacement of the provided lever arm with a 36-inch-long, 5/8-inch-diameter, zinc-coated steel rod. This type of metal rod is available in most hardware stores.
This longer lever arm can be centered in the shaft, and held in that location by wraps of tape on the arm on both sides of the shaft as shown in the photos above and below.
The press is just high enough on its new base to allow this longer arm to be rotated 360 degrees. Whichever end of the arm is the most comfortable at any given time can then be used to press items with the press.
The rubber end caps that came with the original lever arm may be installed on the new one. Hardware stores sell metal rods like the new one we are using.
Using the Newly Modified One-Ton Arbor Press
Ok. You're finished. Go press something!