How to Make Sugar Rockets
Sugar rockets? If you haven't heard of sugar rockets, you're probably not a teenager cruising YouTube. But sugar rockets aren't just for kids. You can also see sugar-fueled rockets at high-power rocketry events where large models are launched thousands of feet into the sky.
Sugar rockets are simple to make and do not require expensive tooling. The fuel they use is relatively safe, simple and inexpensive to make. When launched, they leave a really nice white smoke trail behind them, which can be seen all the way from ground to burnout during the daytime. Sugar rocket motors can also be used in Estes®-type model rockets, or to launch fireworks effects into the night sky.

Completed Sugar Rocket, Ready for Launch
Daytime Flight of a Sugar Rocket
Here's a cross-section of the 1/2-inch ID sugar-fueled motors we'll be making:

Sugar-Fueled Rocket Motor Cross-Section
Here is a list of the materials and equipment we will be using in this project. We'll also be reviewing the materials for each step of the building process as we go along.
Note: enough chemicals and tubes to make 25 Sugar Rockets are contained in Skylighter's KT1403, 4 Oz. Sugar Rocket Kit.
Please read and observe these safety instructions when making rockets. These essays detail important safety precautions for mixing compositions, and for making and storing fireworks devices.
The most important safety precautions are:
*Note: A pinch is precisely that amount of powder which will stay between two fingertips.
Preparing to Mill and Mix Chemicals
These items will be needed as we make the rocket fuel:

Items Needed for Milling Chemicals, and Mixing Rocket Fuel
First, if they are not already fine powders, the potassium nitrate and sorbitol each need to be milled to a fine, talc-like, consistency. The easiest and safest way to do this is to mill them--individually--in a blade-type coffee mill currently available at Walmart for less than $20.
WARNING: Mixtures of chemicals should never be milled in a blade-type mill. These chemicals should only be milled one at a time. The mill must be carefully cleaned out between chemicals to avoid a fire.
Each of the two chemicals must be milled fine enough to easily pass through a 40-mesh screen.
Weighing Chemicals
Using a small digital scale, weigh out the required amount of each chemical into its own paper cup.

Weighing Potassium Nitrate into a Dedicated Cup
Put the weighed amount of the potassium nitrate into the mill. Close it securely, and mill the chemical for two minutes.
Milling the Potassium Nitrate to a Fine Dust
Dump the milled potassium nitrate onto a 40-mesh screen resting on a piece of paper. Clean all of it out of the mill with a small paintbrush. Ensure that all of the chemical will easily pass through the 40-mesh screen by using a gloved hand to rub the chemical gently through the screen.

Screening Milled Potassium Nitrate (40-Mesh Screen)
Repeat this process for the sorbitol.
Both the potassium nitrate and the sorbitol are now milled and on the piece of paper. Put a pinch of the red iron oxide onto the pile. A pinch is that amount of the iron oxide which will stay between two fingertips.
Put the combined pile of chemicals into a mixing tub. Cap the tub tightly and, while holding the lid on securely, shake the tub to mix the fuel.
Putting Chemicals into a Mixing Tub
Put the screen back on top of the piece of paper as before. Open the tub and dump the mixture onto the 40-mesh screen. Gently rub the fuel through the screen with a gloved hand.

Rubbing Fuel Mixture through the 40-Mesh Screen
Put the fuel back into the tub again, close it, and repeat the shaking. Repeat the screening one more time. Intimate mixing of the chemicals is important for the fuel to work well in rocket motors.
Put the fuel back into the tub once more, seal it, and shake it one more time. The fuel is now ready to use.
The sugar in the fuel composition makes it somewhat "hygroscopic," meaning it will absorb moisture out of the humid air. Keeping the fuel in the tightly sealed tub between uses will help to keep it dry.
Homemade Aluminum and Wood 1/2-Inch Rammers
Cut a piece of either 1/2-inch oak-wood dowel, or aluminum rod, 5-1/2 to 6 inches long. File or sand the ends smooth and flat.
If the wood dowel is used, install a 3/8-inch copper plumbing cap on one end with super-glue. Let the glue dry. The purpose of this cap is to reinforce the end of the wood dowel which we will be pounding on when we ram the clay and fuel into the sugar rocket motor.
Cross drill the rammer with a 3/16-inch hole, 1/4 inch from the end, as shown in the photograph above. A short piece of 3/16-inch aluminum rod or a thin awl will be used as a handle. When we're making the sugar rocket motor, this handle will make it easier to twist the rammer to remove it from the rocket after ramming an increment of clay or fuel.
A quick spray of fast-drying lacquer on the wood dowel will prolong its life and make it smoother, easier to use, and more stain-proof.
We now need to mark the rammer to indicate when fuel or clay has been rammed to the desired heights in the paper tube as we're making a motor.
For this step, we need:
First Alignment Mark on Rammer
Align the paper tube with the sketch, and align the rammer alongside the tube, on top of the sketch as shown in the photo above.
Put a mark on the rammer where the top of the tube will be if the rammer is inserted all the way into the tube. This mark is simply a reference mark to let us know how much clay and/or fuel has been rammed in the motor.

Second Alignment Mark on Rammer
Slide the rammer to the right as in the picture above to align the bottom of the rammer with the joint on the sketch between the clay nozzle and the fuel. Put a mark on the rammer where the top of the tube will be when the rammer is so aligned. This mark will let us know when enough clay has been used to ram the clay nozzle to the correct size.

Third Alignment Mark on Rammer
Slide the rammer to the right again as in the picture above to align the bottom of the rammer with the joint on the sketch between the fuel and the clay bulkhead. Put a mark on the rammer where the top of the tube will be when the rammer is aligned with the top of the fuel grain. This mark lets us know when enough fuel increments have been rammed in the motor.

Fourth Alignment Mark on Rammer
Slide the rammer to the right once more as in the picture above to align the bottom of the rammer with the top of the clay bulkhead. Finally, put a mark on the rammer where the top of the tube will be when the rammer is aligned with the top of the clay bulkhead. This mark will let us know when the clay bulkhead has been rammed to the proper thickness.
Extend these marks all the way around the rammer so that they form rings.

Four Alignment Marks on the Rammer
In the order we made them, these rings should measure 5 inches, 4-1/2 inches, 1 inch, and 3/4 inches from the bottom of the rammer.
The clay and fuel we will be ramming are both fine, loose powders. When the powder has been introduced into the tube and then the rammer is pushed into the tube in preparation for ramming, they tend to "floof up" (that's a technical term) around the rammer and spill out of the tube.
This problem can be eliminated by the use of a 1/2-inch (#10) rubber O-ring. This type of O-ring may be found in the plumbing supplies department of most hardware or home improvement stores. The O-ring should fit snugly enough on the rammer to not fall off, but be just loose enough to allow it to slide easily up and down the rammer.
Simply put the O-ring on the rammer and push it down toward the bottom of the rammer before ramming each increment. As the rammer is pushed into the tube, the O-ring will ride up, sealing the gap where the top of the tube meets the rammer. This will prevent much of the dust from escaping out of that gap.

Rubber O-Ring Installed on Rammer
Materials Assembled for Ramming the Nozzle Clay
We'll be ramming the clay rocket nozzle solid, with no hole through it yet, and then drilling the hole later. Yes, the dry, powdered clay will ram into a nice, solid clay plug during the following process. Do not wet it.
Ramming Nozzle Clay
Seal one end of the paper tube with masking tape.
Put a rounded 1/2-teaspoonful of the clay into the tube through the funnel.
Put the bottom of the paper tube on the ramming block on top of the ramming post.
Slide the rammer, with the o-ring on it, into the paper tube until it has compressed the clay as much as possible.
Ram the nozzle clay with 12-13 solid whacks of the mallet. The second Sharpie mark on the rammer should be right at the top of the tube indicating that the rammer is at the top of the nozzle.
You should be able to feel a very slight bulge in the sides of the paper tube where the top of the nozzle clay is. That indicates that the clay has been rammed solidly enough. If there is no bulge, ram the clay a little more and a bit more solidly. If the tube splits in that area, you've rammed the clay with too much force. You need to try again with a fresh tube, and back off with the pressure of the ramming a little bit. This skill takes some "getting the feel of it" to get good at it.
Remove the rammer, and tap any excess clay back into its plastic tub.
Materials for Ramming Fuel Increments
The only additional materials needed for this step are:
Assembled Materials for Ramming Fuel Increments
We will be ramming increments of fuel into the paper tube in the same way we rammed the nozzle clay increment. Ideally, each rammed increment of fuel should end up being about 1/4 inch to 3/8 inch thick.
Open the fuel tub and scoop about 1/4-cup of the fuel into the paper cup. Reseal the fuel tub and set it aside. Minimizing the amount of open, exposed fuel in this way is a very important safety precaution. Make sure there are no other exposed compositions or finished devices in your work area.
Wear a leather glove to protect the hand which will be steadying the paper tube as the fuel is rammed. Safety glasses when working with combustible compositions are a must also.
Put a rounded 1/4-teaspoonful of the fuel into the paper tube through the funnel.
Ram that increment of fuel with about six solid whacks with the mallet. Notice how tall that increment of rammed fuel is by checking how far the "top of the nozzle clay" alignment mark is now above the top of the tube. It should be about 1/4 inch to 3/8 inch above it. Adjust the amount of fuel in the increments that follow as necessary to consistently produce rammed-fuel increments of 1/4-inch to 3/8-inch height.
Repeat the ramming of fuel increments until the third Sharpie mark on the rammer is aligned with the top of the tube. This tells you that the rammer is now at the top of the fuel grain.
All the required fuel has now been rammed in the motor tube. Tap any excess fuel in the tube back into the cup of fuel, and put the remaining fuel in the paper cup back into the plastic tub of fuel and tightly seal it.
Ramming the Clay Bulkhead
To ram the clay bulkhead, simply load a slightly rounded 1/4-teaspoonful of the bentonite clay into the tube. Ram it with eight solid mallet blows. The final, fourth rammer alignment mark should now be aligned with the top of the tube.

Clay Bulkhead Rammed in Rocket Motor Tube
In the next step we will hand-drill that needed hollow core. But first we need to make a drilling jig to ensure that the drill makes the core straight into the motor, parallel with the tube's axis.
To make this jig, we need the following materials:
Materials for Making Core-Drilling Jig
To make the drill jig, measure up 3-1/4 inches from the sharp end of the drill bit and make a little pencil mark there on the bit.
Start wrapping duct-tape onto the drill bit with the edge of the tape nearer the sharp tip aligned with the mark you made on the bit at 3-1/4 inches. Looking at the sharp end of the bit, the tape should wrap on in a clockwise direction. This will help prevent the tape from unwrapping later as the wrapped bit is being twisted inside the 3/4-inch ID tube.
Wrap the duct tape onto the drill bit slowly and smoothly until the OD of the tape wrap approaches 3/4 inch.
Cut the tape off and smooth the wraps down. See if the tape-wrapped bit just fits into the 3/4-inch ID paper tube. The tape-wrapped bit should just fit snugly into the paper tube, but turn easily in the tube once it's inside it. If the fit is too loose, add another turn or two of the tape. If the fit is too tight, remove a turn or two of the tape.
The drilling jig works as shown in the sketch below. The larger-diameter tube, and the tape-wraps on the drill bit, work together to keep the bit centered and parallel with the rocket-motor tube as the core is being drilled.

How Drilling Jig Works to Keep Drill Bit Centered and Straight
Materials Readied for Drilling Rocket Motor Core
These materials are needed to drill the hollow core into the rocket motor:
Drilling Hollow Core
Looking at the nozzle-end of the rocket motor, the clay there is flush with the end of the tube. Remove the masking tape from that end if you haven't already done so.
Using a sharp awl, make a little dent right in the center of the clay surface. Tap any excess clay removed during this step and during the steps that follow into the paper cup.

Making Dent in Center of Nozzle Clay with an Awl
Using a sharp 1/8-inch drill bit, hand-twist-drill a hole centered at that dent in the clay. Drill this hole 1/8 inch deep.

1/8-Inch Hole Drilled 1/8 inch Deep in Center of Nozzle Clay
Expand that centering hole to 1/4-inch diameter with the 1/4-inch drill-jig drill bit.

Center-Hole Enlarged to 1/4-Inch Diameter
Use the sharp razor knife to trim the sharp edge of the hole and the remaining flat end of the nozzle clay into a slight "cone" or "funnel" shape, forming a "divergent" exterior to the clay nozzle. This center hole and tapered area will guide the 1/4-inch bit straight into the nozzle in the next step.

Creating Funnel Shape to Nozzle Exterior Surface with Knife
Slide the rocket motor halfway into the large paper tube, with the nozzle inside the 3/4-inch tube. Insert the tape-wrapped drill bit into the other end of the 3/4-inch tube. You should be able to feel when the drill bit centers up on the face of the clay nozzle, and slides into the pre-drilled 1/4-inch hole in the clay.
Begin hand-twist-drilling the bit into the nozzle clay. Periodically remove the bit from the tube and tap the excess clay into the paper cup. Repeat this until you start to see pink fuel dust coming out of the tube.

Rocket Motor and Tape-Wrapped 1/4-Inch Drill Bit Inserted into Large Paper Tube
Dump the accumulated loose clay in the paper cup back into the tub of clay.
Continue drilling into the fuel grain, gently hand-twisting the drill bit. Periodically remove the bit and dump the loose fuel into the paper cup. This is where the new, sharp drill bit will earn its keep with quick and easy drilling.
Continue drilling into the fuel grain until the hollow core is at least two inches deep. At this point, the hole you have created is sufficiently long to accurately direct the drill during the rest of the drilling process without the help of the paper tube

Hollow Core Drilled At Least Two inches into Motor
Remove the large paper tube from the motor, and continue drilling until the duct-tape wrap bottoms out on the end of the motor. The hollow core is now 3-1/4 inches deep.
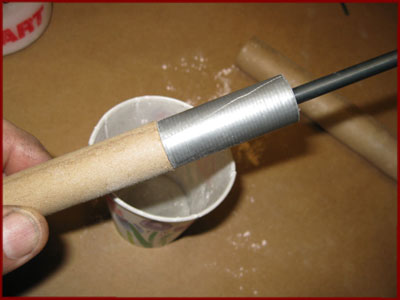
Duct Tape Bottomed Out on Paper Tube
Clean any excess fuel dust out of the core, and off the drill bit, and dump the loose fuel back into the tub of fuel, tightly resealing it.

Completed Hollow Core in Rocket Motor
Materials needed in this step:
Materials for Installing Stick on Rocket Motor
Home Depot, Lowes, and similar hardware/lumber stores sell 1/4-inch-square, 36-inch-long "square dowels" in the lumber/molding department. We'll be cutting one of these in half to produce two 18-inch rocket sticks.
Find the center of the stick by balancing it on a finger. Cut the stick in half diagonally, as shown in the photo above.
Attach the stick to the nozzle end of the rocket motor with at least 2 inches of the beveled end of the stick lapped onto the motor as shown in the photo below.

Holding the Rocket Stick on the Nozzle End of the Rocket Motor
Tear off eight inches of the masking tape and install it as a band holding the stick onto the motor. Repeat for a second masking-tape band, as shown in the photo below.

Two Masking-Tape Bands Holding Stick onto Motor
Sight down the motor and stick, and twist the stick side-to-side to align it. Be sure it is parallel with the motor for a straight rocket flight.

Sighting and Aligning Rocket Stick and Motor

Materials for Fusing the Rocket Motor
The modified ignition fuse will be installed in the rocket motor as shown in this sketch. The tape wrapping ensures that the fuel grain will be ignited at the top of the hollow core, which will maximize thrust at ignition and takeoff.
How Visco Ignition Fuse is Installed in the Motor
To fuse the rocket motor, cut a piece of the green visco ignition fuse 6 inches long. Put sharpie marks on the fuse in 1 inch and 4 inches from one end.

6-Inch Piece of Visco Fuse, Marked at 1 Inch and 4 Inches
Now, wrap the 3-inch length of fuse between the marks with a rolled-on 3-inch piece of masking tape. Repeat this with two more 3-inch pieces of tape.
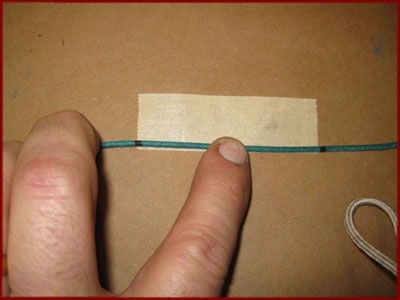
Ready to Roll First 3-Inch Piece of Masking Tape around Fuse

First Piece of Masking Tape Rolled onto Fuse Halfway

Visco Fuse Wrapped with Three 3-Inch Pieces of the Tape
Now, bend 1/2 inch of the exposed 1 inch of fuse back on itself, to double the fuse at that end. That doubled section of fuse will hold the fuse securely in the motor's hollow core.

Bending Fuse End Back on Itself
Then, just insert the fuse into the rocket motor as far as it will go. The rocket is now ready to take out, light, and fly.

Ignition Fuse Inserted into Core of Rocket Motor
Rocket Inserted into Launch Tube and Being Ignited
Sugar rockets are simple to make and do not require expensive tooling. The fuel they use is relatively safe, simple and inexpensive to make. When launched, they leave a really nice white smoke trail behind them, which can be seen all the way from ground to burnout during the daytime. Sugar rocket motors can also be used in Estes®-type model rockets, or to launch fireworks effects into the night sky.

Completed Sugar Rocket, Ready for Launch
Daytime Flight of a Sugar Rocket
Here's a cross-section of the 1/2-inch ID sugar-fueled motors we'll be making:

Sugar-Fueled Rocket Motor Cross-Section
Here is a list of the materials and equipment we will be using in this project. We'll also be reviewing the materials for each step of the building process as we go along.
Note: enough chemicals and tubes to make 25 Sugar Rockets are contained in Skylighter's KT1403, 4 Oz. Sugar Rocket Kit.
- Chemicals:
- Potassium nitrate
- Sorbitol
- Red iron oxide
- A spoon or scoop for measuring chemicals
- A blade type mill or coffee grinder
- A 40-mesh screen
- A digital weighing scale
- Paper cups
- A sheet of paper larger than the 40-mesh screen
- A small paint brush
- Rubber or nitrile gloves
- A dust mask or respirator
- A full-scale copy of the cross-section sketch of the motor
- A 1/2-inch ID, 3/4-inch OD, 5-inch long, paper motor tube (get a bunch -- you're gonna like these rockets)
- A Sharpie marker
- 1-inch-wide masking tape
- Bentonite clay
- A funnel which fits into the paper tube
- A 1/2-teaspoon measuring spoon
- A solid mallet
- A solid "puck" of aluminum or plastic on which to ram the motor
- A solid post on which to do the ramming
- A 1/4-teaspoon measuring spoon
- Leather glove
- A measuring ruler
- A pencil
- 1/4-inch-square, 18-inch-long, stick
- Razor-anvil cutters to cut the stick (e.g., Sears "Handi-Cuts")
- Green visco ignition fuse
- A launch tube about 3 feet long
- A source of ignition, such as a Bernzomatic TS4000 propane torch
- A plastic mixing tub and tight-fitting lid
- 1/2-inch oak-wood dowel or aluminum rod, at least 6 inches long
- A section of 3/16-inch aluminum rod, or an awl, to serve as a handle
- A saw to cut the oak dowel or aluminum rod
- A file or sandpaper to smooth the oak dowel or aluminum rod
- A 3/16-inch drill bit and drill
- A 3/8-inch copper pipe cap (if using oak dowel)
- A 3/4-inch ID, 7-1/2-inch-long paper tube
- A roll of duct tape
- A 1/4-inch diameter, 12-inch-long, brand-new, sharp drill bit
- Sharp awl or small nail
- Sharp 1/8-inch drill bit
- Sharp razor knife
- Safety glasses
- Super Glue (if using oak dowel)
- Spray lacquer (if using oak dowel)
Step 1: Making the Rocket Fuel
Safety Note: Making and using the rocket fuel can be dusty operations. Wearing a dust-mask and performing the steps outdoors can minimize the impact of this dust.Please read and observe these safety instructions when making rockets. These essays detail important safety precautions for mixing compositions, and for making and storing fireworks devices.
The most important safety precautions are:
- always minimize the amount of exposed or open containers of pyrotechnic compositions and devices,
- wear safety glasses,
- wear cotton clothing that covers as much of the body as possible, and
- safely store compositions and devices.
- Potassium nitrate is the oxidizer
- Sorbitol, a sugar found in fruits, is the fuel
- Red iron oxide is a catalyst that enhances burn rate and increases the fuel's thrust
Sugar Rocket Fuel
Component | Percent | Factor | 4.4 oz | 125.5 g |
Potassium nitrate | 65% | 0.65 | 2.6 oz | 73.9 g |
Sorbitol | 35% | 0.35 | 1.4 oz | 39.8 g |
Red iron oxide | A pinch* |
*Note: A pinch is precisely that amount of powder which will stay between two fingertips.
Preparing to Mill and Mix Chemicals
These items will be needed as we make the rocket fuel:
- A printout of the formula above and the following instructions
- The chemicals
- Potassium nitrate
- Sorbitol
- Red iron oxide
- A spoon or scoop for measuring chemicals
- A blade type mill (coffee grinder)
- A 40-mesh screen
- A digital weighing scale
- Paper cups
- A sheet of paper larger than the 40-mesh screen
- A small paint brush
- Rubber or nitrile gloves
- A dust mask or respirator
- A plastic mixing tub and tight-fitting lid

Items Needed for Milling Chemicals, and Mixing Rocket Fuel
First, if they are not already fine powders, the potassium nitrate and sorbitol each need to be milled to a fine, talc-like, consistency. The easiest and safest way to do this is to mill them--individually--in a blade-type coffee mill currently available at Walmart for less than $20.
WARNING: Mixtures of chemicals should never be milled in a blade-type mill. These chemicals should only be milled one at a time. The mill must be carefully cleaned out between chemicals to avoid a fire.
Each of the two chemicals must be milled fine enough to easily pass through a 40-mesh screen.
Weighing Chemicals
Using a small digital scale, weigh out the required amount of each chemical into its own paper cup.

Weighing Potassium Nitrate into a Dedicated Cup
Put the weighed amount of the potassium nitrate into the mill. Close it securely, and mill the chemical for two minutes.
Milling the Potassium Nitrate to a Fine Dust
Dump the milled potassium nitrate onto a 40-mesh screen resting on a piece of paper. Clean all of it out of the mill with a small paintbrush. Ensure that all of the chemical will easily pass through the 40-mesh screen by using a gloved hand to rub the chemical gently through the screen.

Screening Milled Potassium Nitrate (40-Mesh Screen)
Repeat this process for the sorbitol.
Both the potassium nitrate and the sorbitol are now milled and on the piece of paper. Put a pinch of the red iron oxide onto the pile. A pinch is that amount of the iron oxide which will stay between two fingertips.
Put the combined pile of chemicals into a mixing tub. Cap the tub tightly and, while holding the lid on securely, shake the tub to mix the fuel.
Putting Chemicals into a Mixing Tub
Put the screen back on top of the piece of paper as before. Open the tub and dump the mixture onto the 40-mesh screen. Gently rub the fuel through the screen with a gloved hand.

Rubbing Fuel Mixture through the 40-Mesh Screen
Put the fuel back into the tub again, close it, and repeat the shaking. Repeat the screening one more time. Intimate mixing of the chemicals is important for the fuel to work well in rocket motors.
Put the fuel back into the tub once more, seal it, and shake it one more time. The fuel is now ready to use.
The sugar in the fuel composition makes it somewhat "hygroscopic," meaning it will absorb moisture out of the humid air. Keeping the fuel in the tightly sealed tub between uses will help to keep it dry.
Option #1: If you already have tools:
Steps 2 -- 7: If you are using Skylighter's TL1204 Rocket Toolset, you should skip steps 2 - 7. Instead, follow the instructions for making black powder rockets, and simply substitute sugar rocket fuel for black powder fuel.Option #2: If you are making your own tools:
Step 2: Making and Marking the Rocket Motor Rammer
For this step, you will need:- 1/2-inch oak-wood dowel or aluminum rod, at least 6 inches long
- A saw to cut that material
- A file or sandpaper to smooth that material
- A 3/16-inch drill bit and drill
- A 3/8-inch copper pipe cap for wood rammer
- Super Glue for wood rammer
- Spray lacquer for finishing the wood rammer
- A section of 3/16-inch aluminum rod, or an awl, to serve as a handle
Homemade Aluminum and Wood 1/2-Inch Rammers
Cut a piece of either 1/2-inch oak-wood dowel, or aluminum rod, 5-1/2 to 6 inches long. File or sand the ends smooth and flat.
If the wood dowel is used, install a 3/8-inch copper plumbing cap on one end with super-glue. Let the glue dry. The purpose of this cap is to reinforce the end of the wood dowel which we will be pounding on when we ram the clay and fuel into the sugar rocket motor.
Cross drill the rammer with a 3/16-inch hole, 1/4 inch from the end, as shown in the photograph above. A short piece of 3/16-inch aluminum rod or a thin awl will be used as a handle. When we're making the sugar rocket motor, this handle will make it easier to twist the rammer to remove it from the rocket after ramming an increment of clay or fuel.
A quick spray of fast-drying lacquer on the wood dowel will prolong its life and make it smoother, easier to use, and more stain-proof.
We now need to mark the rammer to indicate when fuel or clay has been rammed to the desired heights in the paper tube as we're making a motor.
For this step, we need:
- A full-scale copy of the cross-section sketch of the motor
- A 1/2-inch ID, 5-inch long, paper tube
- The rammer
- A Sharpie marker
- A measuring ruler
Align the paper tube with the sketch, and align the rammer alongside the tube, on top of the sketch as shown in the photo above.
Put a mark on the rammer where the top of the tube will be if the rammer is inserted all the way into the tube. This mark is simply a reference mark to let us know how much clay and/or fuel has been rammed in the motor.

Second Alignment Mark on Rammer
Slide the rammer to the right as in the picture above to align the bottom of the rammer with the joint on the sketch between the clay nozzle and the fuel. Put a mark on the rammer where the top of the tube will be when the rammer is so aligned. This mark will let us know when enough clay has been used to ram the clay nozzle to the correct size.

Third Alignment Mark on Rammer
Slide the rammer to the right again as in the picture above to align the bottom of the rammer with the joint on the sketch between the fuel and the clay bulkhead. Put a mark on the rammer where the top of the tube will be when the rammer is aligned with the top of the fuel grain. This mark lets us know when enough fuel increments have been rammed in the motor.

Fourth Alignment Mark on Rammer
Slide the rammer to the right once more as in the picture above to align the bottom of the rammer with the top of the clay bulkhead. Finally, put a mark on the rammer where the top of the tube will be when the rammer is aligned with the top of the clay bulkhead. This mark will let us know when the clay bulkhead has been rammed to the proper thickness.
Extend these marks all the way around the rammer so that they form rings.

Four Alignment Marks on the Rammer
In the order we made them, these rings should measure 5 inches, 4-1/2 inches, 1 inch, and 3/4 inches from the bottom of the rammer.
The clay and fuel we will be ramming are both fine, loose powders. When the powder has been introduced into the tube and then the rammer is pushed into the tube in preparation for ramming, they tend to "floof up" (that's a technical term) around the rammer and spill out of the tube.
This problem can be eliminated by the use of a 1/2-inch (#10) rubber O-ring. This type of O-ring may be found in the plumbing supplies department of most hardware or home improvement stores. The O-ring should fit snugly enough on the rammer to not fall off, but be just loose enough to allow it to slide easily up and down the rammer.
Simply put the O-ring on the rammer and push it down toward the bottom of the rammer before ramming each increment. As the rammer is pushed into the tube, the O-ring will ride up, sealing the gap where the top of the tube meets the rammer. This will prevent much of the dust from escaping out of that gap.

Rubber O-Ring Installed on Rammer
Step 3: Ramming the Clay for the Rocket Nozzle
For this step, we'll need:- 1/2-inch ID, 3/4-inch OD, 5-inch-long paper tube
- 1-inch-wide masking tape
- Bentonite clay
- The rammer
- A funnel which fits into the paper tube
- A 1/2-teaspoon measuring spoon
- A solid mallet
- A solid piece of aluminum or plastic on which to ram the motor
- A solid post on which to do the ramming
Materials Assembled for Ramming the Nozzle Clay
We'll be ramming the clay rocket nozzle solid, with no hole through it yet, and then drilling the hole later. Yes, the dry, powdered clay will ram into a nice, solid clay plug during the following process. Do not wet it.
Ramming Nozzle Clay
Seal one end of the paper tube with masking tape.
Put a rounded 1/2-teaspoonful of the clay into the tube through the funnel.
Put the bottom of the paper tube on the ramming block on top of the ramming post.
Slide the rammer, with the o-ring on it, into the paper tube until it has compressed the clay as much as possible.
Ram the nozzle clay with 12-13 solid whacks of the mallet. The second Sharpie mark on the rammer should be right at the top of the tube indicating that the rammer is at the top of the nozzle.
You should be able to feel a very slight bulge in the sides of the paper tube where the top of the nozzle clay is. That indicates that the clay has been rammed solidly enough. If there is no bulge, ram the clay a little more and a bit more solidly. If the tube splits in that area, you've rammed the clay with too much force. You need to try again with a fresh tube, and back off with the pressure of the ramming a little bit. This skill takes some "getting the feel of it" to get good at it.
Remove the rammer, and tap any excess clay back into its plastic tub.
Step #4: Ramming Increments of Fuel in the Sugar Rocket Motor Tube
Materials for Ramming Fuel Increments
The only additional materials needed for this step are:
- The sealed tub of rocket fuel
- One of the paper cups
- A 1/4-teaspoon measuring spoon
- Leather glove for the hand which will be steadying the motor tube as the fuel is rammed
Assembled Materials for Ramming Fuel Increments
We will be ramming increments of fuel into the paper tube in the same way we rammed the nozzle clay increment. Ideally, each rammed increment of fuel should end up being about 1/4 inch to 3/8 inch thick.
Open the fuel tub and scoop about 1/4-cup of the fuel into the paper cup. Reseal the fuel tub and set it aside. Minimizing the amount of open, exposed fuel in this way is a very important safety precaution. Make sure there are no other exposed compositions or finished devices in your work area.
Wear a leather glove to protect the hand which will be steadying the paper tube as the fuel is rammed. Safety glasses when working with combustible compositions are a must also.
Put a rounded 1/4-teaspoonful of the fuel into the paper tube through the funnel.
Ram that increment of fuel with about six solid whacks with the mallet. Notice how tall that increment of rammed fuel is by checking how far the "top of the nozzle clay" alignment mark is now above the top of the tube. It should be about 1/4 inch to 3/8 inch above it. Adjust the amount of fuel in the increments that follow as necessary to consistently produce rammed-fuel increments of 1/4-inch to 3/8-inch height.
Repeat the ramming of fuel increments until the third Sharpie mark on the rammer is aligned with the top of the tube. This tells you that the rammer is now at the top of the fuel grain.
All the required fuel has now been rammed in the motor tube. Tap any excess fuel in the tube back into the cup of fuel, and put the remaining fuel in the paper cup back into the plastic tub of fuel and tightly seal it.
Step #5: Ramming the Clay Bulkhead in the Motor
Ramming the Clay Bulkhead
To ram the clay bulkhead, simply load a slightly rounded 1/4-teaspoonful of the bentonite clay into the tube. Ram it with eight solid mallet blows. The final, fourth rammer alignment mark should now be aligned with the top of the tube.

Clay Bulkhead Rammed in Rocket Motor Tube
Step #6: Making the Core-Drilling Jig
The nozzle clay and fuel grain in this motor have been rammed solid, without the hollow core shown in the motor cross-section sketch. If the motor had been rammed with 1/2-inch, black-powder rocket tooling--which would work well, by the way--the long spindle of that tooling would have created the necessary hollow core.In the next step we will hand-drill that needed hollow core. But first we need to make a drilling jig to ensure that the drill makes the core straight into the motor, parallel with the tube's axis.
To make this jig, we need the following materials:
- A 3/4-inch ID, 7-1/2-inch-long paper tube which just slips over the OD of our rammed 1/2-inch motor
- A roll of duct tape
- A 1/4-inch diameter, 12-inch-long, brand-new, sharp drill bit (Home Depot and Lowes sell these)
- A measuring ruler
- A pencil
To make the drill jig, measure up 3-1/4 inches from the sharp end of the drill bit and make a little pencil mark there on the bit.
Start wrapping duct-tape onto the drill bit with the edge of the tape nearer the sharp tip aligned with the mark you made on the bit at 3-1/4 inches. Looking at the sharp end of the bit, the tape should wrap on in a clockwise direction. This will help prevent the tape from unwrapping later as the wrapped bit is being twisted inside the 3/4-inch ID tube.
Wrap the duct tape onto the drill bit slowly and smoothly until the OD of the tape wrap approaches 3/4 inch.
Cut the tape off and smooth the wraps down. See if the tape-wrapped bit just fits into the 3/4-inch ID paper tube. The tape-wrapped bit should just fit snugly into the paper tube, but turn easily in the tube once it's inside it. If the fit is too loose, add another turn or two of the tape. If the fit is too tight, remove a turn or two of the tape.
The drilling jig works as shown in the sketch below. The larger-diameter tube, and the tape-wraps on the drill bit, work together to keep the bit centered and parallel with the rocket-motor tube as the core is being drilled.

How Drilling Jig Works to Keep Drill Bit Centered and Straight
Step #7: Drilling the Hollow Core in the Rocket Motor
Materials Readied for Drilling Rocket Motor Core
These materials are needed to drill the hollow core into the rocket motor:
- Rocket motor
- Sharp awl or small nail
- Sharp 1/8-inch drill bit
- Sharp razor knife
- Drill jig with tape-wrapped 1/4-inch drill bit, and paper tube as above
- Leather glove
- Safety glasses
- Bentonite clay tub
- Fuel tub
- Paper cup
Looking at the nozzle-end of the rocket motor, the clay there is flush with the end of the tube. Remove the masking tape from that end if you haven't already done so.
Using a sharp awl, make a little dent right in the center of the clay surface. Tap any excess clay removed during this step and during the steps that follow into the paper cup.

Making Dent in Center of Nozzle Clay with an Awl
Using a sharp 1/8-inch drill bit, hand-twist-drill a hole centered at that dent in the clay. Drill this hole 1/8 inch deep.

1/8-Inch Hole Drilled 1/8 inch Deep in Center of Nozzle Clay
Expand that centering hole to 1/4-inch diameter with the 1/4-inch drill-jig drill bit.

Center-Hole Enlarged to 1/4-Inch Diameter
Use the sharp razor knife to trim the sharp edge of the hole and the remaining flat end of the nozzle clay into a slight "cone" or "funnel" shape, forming a "divergent" exterior to the clay nozzle. This center hole and tapered area will guide the 1/4-inch bit straight into the nozzle in the next step.

Creating Funnel Shape to Nozzle Exterior Surface with Knife
Slide the rocket motor halfway into the large paper tube, with the nozzle inside the 3/4-inch tube. Insert the tape-wrapped drill bit into the other end of the 3/4-inch tube. You should be able to feel when the drill bit centers up on the face of the clay nozzle, and slides into the pre-drilled 1/4-inch hole in the clay.
Begin hand-twist-drilling the bit into the nozzle clay. Periodically remove the bit from the tube and tap the excess clay into the paper cup. Repeat this until you start to see pink fuel dust coming out of the tube.

Rocket Motor and Tape-Wrapped 1/4-Inch Drill Bit Inserted into Large Paper Tube
Dump the accumulated loose clay in the paper cup back into the tub of clay.
Continue drilling into the fuel grain, gently hand-twisting the drill bit. Periodically remove the bit and dump the loose fuel into the paper cup. This is where the new, sharp drill bit will earn its keep with quick and easy drilling.
Continue drilling into the fuel grain until the hollow core is at least two inches deep. At this point, the hole you have created is sufficiently long to accurately direct the drill during the rest of the drilling process without the help of the paper tube

Hollow Core Drilled At Least Two inches into Motor
Remove the large paper tube from the motor, and continue drilling until the duct-tape wrap bottoms out on the end of the motor. The hollow core is now 3-1/4 inches deep.
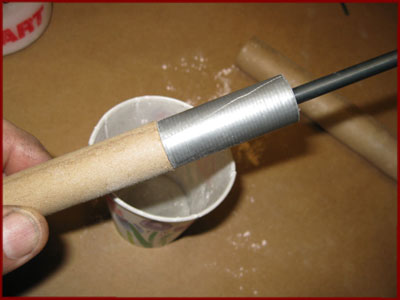
Duct Tape Bottomed Out on Paper Tube
Clean any excess fuel dust out of the core, and off the drill bit, and dump the loose fuel back into the tub of fuel, tightly resealing it.

Completed Hollow Core in Rocket Motor
Step #8: Installing the Stick on the Rocket Motor
These rockets are stick-stabilized, meaning that a simple stick is used to keep the rocket flying straight in the desired direction at launch and during flight.Materials needed in this step:
- Rocket motor
- 1/4-inch-square, 18-inch-long, stick
- 1-inch-wide masking tape
- Razor-anvil cutters to cut the stick (or a different cutting tool)
Materials for Installing Stick on Rocket Motor
Home Depot, Lowes, and similar hardware/lumber stores sell 1/4-inch-square, 36-inch-long "square dowels" in the lumber/molding department. We'll be cutting one of these in half to produce two 18-inch rocket sticks.
Find the center of the stick by balancing it on a finger. Cut the stick in half diagonally, as shown in the photo above.
Attach the stick to the nozzle end of the rocket motor with at least 2 inches of the beveled end of the stick lapped onto the motor as shown in the photo below.

Holding the Rocket Stick on the Nozzle End of the Rocket Motor
Tear off eight inches of the masking tape and install it as a band holding the stick onto the motor. Repeat for a second masking-tape band, as shown in the photo below.

Two Masking-Tape Bands Holding Stick onto Motor
Sight down the motor and stick, and twist the stick side-to-side to align it. Be sure it is parallel with the motor for a straight rocket flight.

Sighting and Aligning Rocket Stick and Motor
Step #9: Installing the Ignition Fuse in the Rocket Motor
These materials are necessary for this step:- Green visco ignition fuse
- Razor-cutter to cut fuse (never use scissors)
- 1-inch-wide masking tape
- Measuring ruler
- Sharpie marker
- The rocket motor with stick

Materials for Fusing the Rocket Motor
The modified ignition fuse will be installed in the rocket motor as shown in this sketch. The tape wrapping ensures that the fuel grain will be ignited at the top of the hollow core, which will maximize thrust at ignition and takeoff.
How Visco Ignition Fuse is Installed in the Motor
To fuse the rocket motor, cut a piece of the green visco ignition fuse 6 inches long. Put sharpie marks on the fuse in 1 inch and 4 inches from one end.

6-Inch Piece of Visco Fuse, Marked at 1 Inch and 4 Inches
Now, wrap the 3-inch length of fuse between the marks with a rolled-on 3-inch piece of masking tape. Repeat this with two more 3-inch pieces of tape.
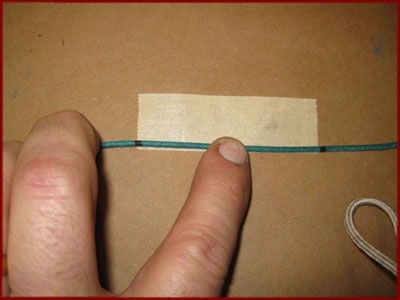
Ready to Roll First 3-Inch Piece of Masking Tape around Fuse

First Piece of Masking Tape Rolled onto Fuse Halfway

Visco Fuse Wrapped with Three 3-Inch Pieces of the Tape
Now, bend 1/2 inch of the exposed 1 inch of fuse back on itself, to double the fuse at that end. That doubled section of fuse will hold the fuse securely in the motor's hollow core.

Bending Fuse End Back on Itself
Then, just insert the fuse into the rocket motor as far as it will go. The rocket is now ready to take out, light, and fly.

Ignition Fuse Inserted into Core of Rocket Motor
Step 10: Installing Rocket in Launch Tube, and Flying the Rocket
For this final, fun step of the rocket process, all that is needed is:- The rocket
- A launch tube about 3 feet long
- A source of ignition, such as a Bernzomatic TS4000 propane torch (lighting visco fuse with a cigarette lighter or a match usually results in a burned thumb from the fuse-fire)